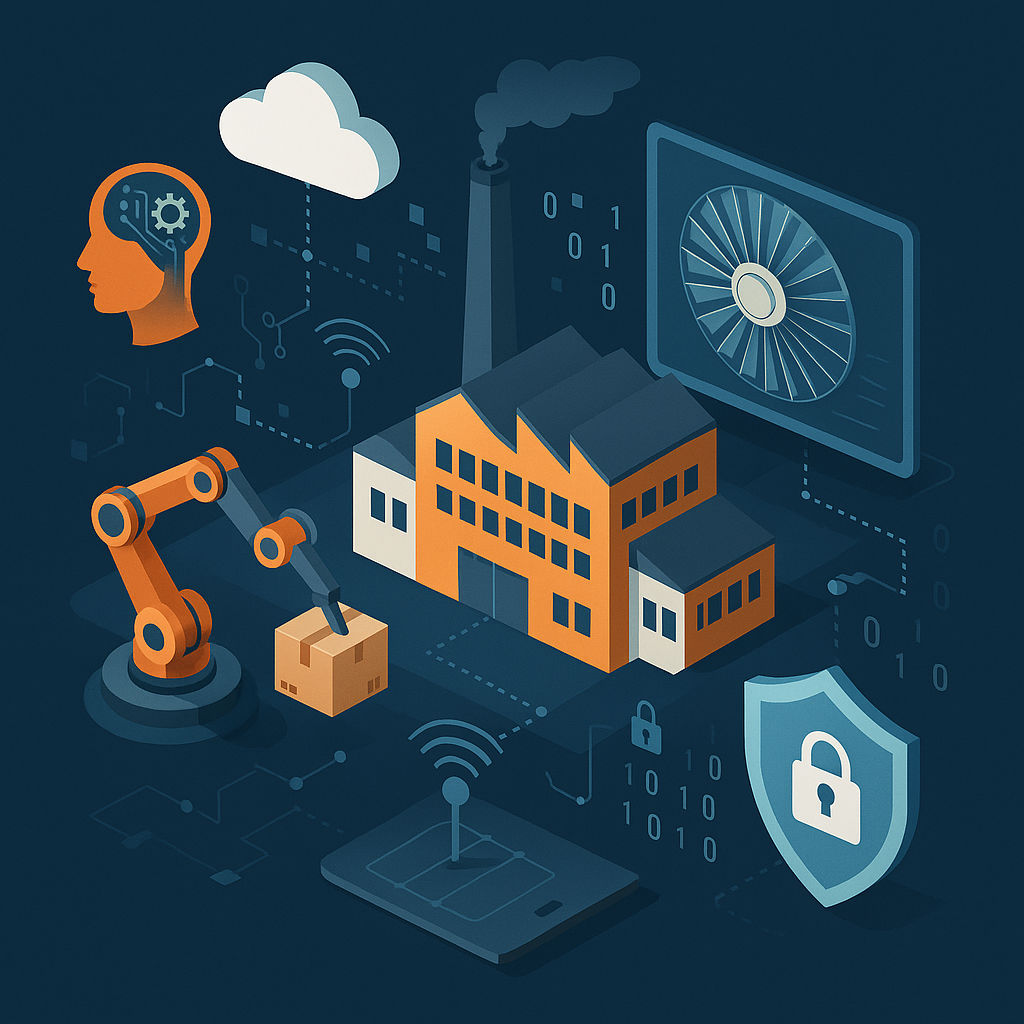
Welcome to the Fourth Industrial Revolution, better known as Industry 4.0. This new era marks a profound shift in the way products are designed, manufactured, and distributed. Powered by automation, data exchange, and intelligent technologies, Industry 4.0 is transforming the very core of manufacturing processes.
But this revolution didn't happen overnight. It builds upon the foundations laid by previous industrial eras:
- The First Industrial Revolution introduced mechanization and steam power, transitioning societies from agriculture to industry.
- The Second brought electricity, oil, and mass production through inventions like the telephone and automobile.
- The Third ushered in electronics, computing, and early automation, with robotics and nuclear energy playing key roles.
- The Fourth now integrates AI, the Internet of Things (IoT), cloud computing, and extended reality, creating smarter, faster, and more interconnected factories.
These advances are not only transforming production but also reshaping entire economies and the way we live and work.
The Technologies Driving Industry 4.0
At the heart of Industry 4.0 is a suite of advanced technologies working together to enable smarter manufacturing:
- Internet of things (IoT) connects physical devices via sensors and networks, enabling real-time data sharing and monitoring.
- AI and Machine Learning help companies harness vast data across their operations for predictive maintenance, optimization, and automation.
- Robotics enhances productivity by automating repetitive tasks, improving quality, and ensuring safer workplaces.
- Cloud Computing supports agile, scalable operations with seamless access to data and applications.
- Cybersecurity becomes essential as IT and OT systems integrate, demanding robust protections against evolving threats.
- Digital Twins provide virtual models of assets and systems, enabling simulation, testing, and better decision-making.
- Edge Computing allows faster data processing close to the source thus reducing latency and improving responsiveness.
When Connectivity Becomes a Risk
While connectivity is the engine behind Industry 4.0, it also introduces new cybersecurity challenges. Every connected machine, system, or third-party component becomes a potential entry point for attackers.
Many factories still run on outdated, unpatched systems that were never built to handle today's digital complexity. Add to that unfamiliar or external components and the risks grow even further. A false sense of security lingers around the idea that operational systems are "safe" simply because they were once isolated. But with IoT and remote access, isolation is no longer a reality.
Even more concerning is the human factor. Many operators and engineers lack formal cybersecurity training, making them easy targets for social engineering, poor password practices, and unintentional security breaches.
Real-World Impact: It’s Already Happening
These risks aren’t theoretical. In Poland, a simple and cheap radio transmitter was enough to hijack railway systems, bringing 20 trains to a halt by spoofing emergency stop signals. No advanced hacking tools, just a vulnerability in legacy technology.
Such incidents highlight just how exposed industrial environments can be. The consequences?
- Financial losses from halted production
- Reputational damage to the brand
- Physical safety risks for workers and the public
As smart factories grow more complex, cybersecurity becomes not just a priority, but a necessity.
IT vs. OT: Bridging the Security Gap
Traditionally, IT (Information Technology) and OT (Operational Technology) operated in silos:
- IT protects digital assets like servers, data, and networks with a focus on confidentiality.
- OT ensures the availability and safety of physical equipment like sensors, machinery, and control systems.
However, Industry 4.0 blurs these lines. OT systems are now connected to IT networks, erasing the air gap that once kept them safe. This convergence demands unified cybersecurity strategies that address both domains.
Organizations are shifting toward shared tools (like firewalls, decisional dashboards, etc), and forming collaborative IT/OT teams to manage risks, incidents, and compliance under a single governance framework.
To address the growing complexity of Industry 4.0, manufacturers need more than just cybersecurity tools — they need clarity. This means understanding business requirements, making informed decisions, qualifying third-party connected products, and assessing the overall level of security maturity. To achieve this, it is essential to approach these actions through the lens of risk. Conducting a risk analysis helps identify the asset, define its security requirements, and uncover surrounding vulnerabilities. And to effectively support this continuous improvement process, all actions should be centralized within a single, unified platform to ensure optimal governance of security requirements.
A Strategic Response: Oligo.RM, the Smart Choice
That’s exactly where Oligo.RM steps in, offering flexible, adaptive risk management tailored to the real challenges of today’s industrial environments.
Tailored especially for complex industries, Oligo.RM supports organizations by:
- Identifying and evaluating risks across both physical and digital infrastructures
- Adapting to operations of all sizes, from small factories to global smart plants
- Supporting governance and regulatory compliance
- Enabling collaboration between IT, OT, and executive teams to embed security at every level
Ultimately, no digital transformation is complete without a thorough risk analysis, because understanding your vulnerabilities is the first step to securing what matters most. In industrial environments where the impact of a breach is amplified, Oligo.RM isn’t just helpful, it’s essential. It empowers companies to stay secure, resilient, and competitive in a rapidly evolving digital landscape.